Introduction
Laser glass and laser crystals serve as the two fundamental gain media in laser technology, each exhibiting distinct optical properties, manufacturing processes, and application domains. These materials play pivotal roles in diverse laser systems, catering to specific performance requirements. This article provides an in-depth comparative analysis of laser glass and laser crystals, examining their material characteristics, fabrication techniques, advantages and limitations, and practical applications. By exploring these aspects, we aim to offer a clearer understanding of their respective contributions to laser advancements.
Comparison of Material Properties
Laser Glass:
Laser glass is primarily composed of phosphate or silicate glass matrices doped with rare-earth ions such as neodymium (Nd³⁺), erbium (Er³⁺), or ytterbium (Yb³⁺) to enable laser amplification. One of its key advantages is its ability to accommodate high doping concentrations, which enhances gain efficiency. Additionally, laser glass exhibits a broad emission spectrum, making it suitable for ultrafast and tunable laser systems. However, its amorphous structure results in lower thermal conductivity, leading to significant thermal effects under high-power operation, such as thermal lensing and beam distortion.
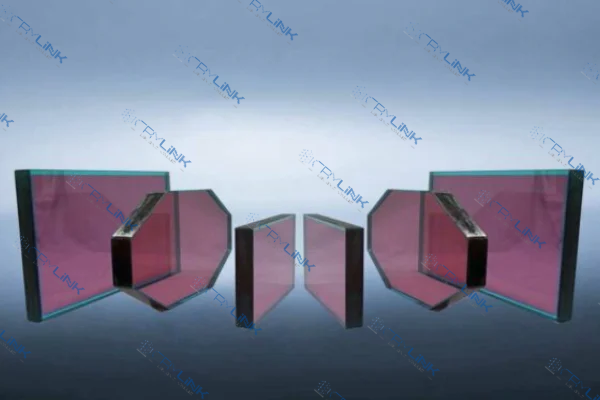
Laser Crystals:
In contrast, laser crystals, including well-known materials like Nd:YAG (neodymium-doped yttrium aluminum garnet), Ti:sapphire (titanium-doped sapphire), and Yb:YVO₄ (ytterbium-doped yttrium orthovanadate), are crystalline in nature. Their ordered atomic structure grants them superior optical homogeneity, high thermal conductivity, and excellent mechanical stability. These properties allow laser crystals to sustain higher power densities with minimal thermal distortion, making them ideal for precision and high-energy applications. However, their production is more complex and costly, and their size is often constrained by crystal growth limitations.
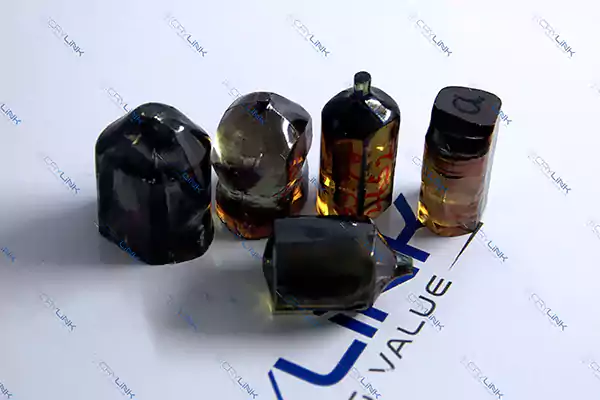
Comparison of Preparation Methods
Laser Glass Fabrication:
The manufacturing of laser glass typically involves the melt-quenching technique, where raw materials are melted at high temperatures and then rapidly cooled to form a homogeneous glass structure. This process is relatively cost-effective and scalable, enabling the production of large-sized components—an essential requirement for high-energy laser systems like those used in inertial confinement fusion (ICF). The flexibility in doping concentrations allows for tailored laser performance. However, the inherent disorder in glass microstructure leads to slight optical inhomogeneities, which can affect beam quality in high-precision applications.
Laser Crystal Growth:
Laser crystals are produced using sophisticated single-crystal growth methods, such as:
- Czochralski (pulling) method – Used for Nd:YAG and Ti:sapphire, producing high-quality single crystals with excellent optical properties.
- Bridgman method – Suitable for certain fluoride and oxide crystals.
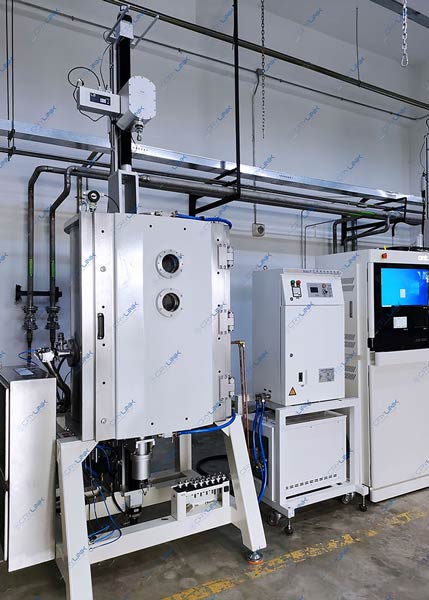
While these methods yield crystals with outstanding thermal and optical performance, they are time-consuming, require stringent process control, and are significantly more expensive than glass production. Additionally, the maximum achievable crystal size is limited, restricting their use in large-aperture laser amplifiers.
Advantages and Disadvantages Analysis
Laser Glass: Strengths and Limitations
Advantages:
Cost-Effectiveness: The melt-quenching process is simpler and more economical, making laser glass ideal for large-scale and high-volume production.
High Doping Flexibility: Rare-earth ions can be incorporated at higher concentrations than in crystals, enhancing laser gain and efficiency.
Broadband Emission: The amorphous structure provides a wider gain spectrum, beneficial for ultrafast and tunable lasers.
Scalability: Large glass slabs can be fabricated for high-energy laser amplifiers, such as those in fusion research.
Disadvantages:
Low Thermal Conductivity: Prone to thermal lensing and beam degradation under high-power operation.
Optical Inhomogeneity: Slight variations in refractive index due to the disordered structure can reduce beam quality.
Lower Damage Threshold: Compared to crystals, glass is more susceptible to optical damage at extreme power levels.
Laser Crystals: Strengths and Limitations
Advantages:
Superior Thermal Management: High thermal conductivity (e.g., ~10 W/m·K for Nd:YAG) minimizes heat-induced distortions, enabling stable high-power operation.
Excellent Optical Quality: The crystalline structure ensures high beam uniformity and low nonlinear losses.
High Damage Resistance: Withstands intense laser fluxes, making them suitable for industrial and military applications.
Precision Performance: Ideal for applications requiring narrow linewidths and high beam quality, such as scientific lasers and medical devices.
Disadvantages:
High Production Cost: Crystal growth is slow, energy-intensive, and requires advanced equipment.
Size Constraints: Difficult to produce large single crystals, limiting their use in high-energy amplifiers.
Limited Doping Flexibility: Some crystals (e.g., Yb:YAG) have lower doping capacities compared to glass.
Comparison of Application Scenarios
High-energy lasers: Phosphate laser glass is used in ICF systems, while Nd:YAG is employed in solid-state laser weapons.
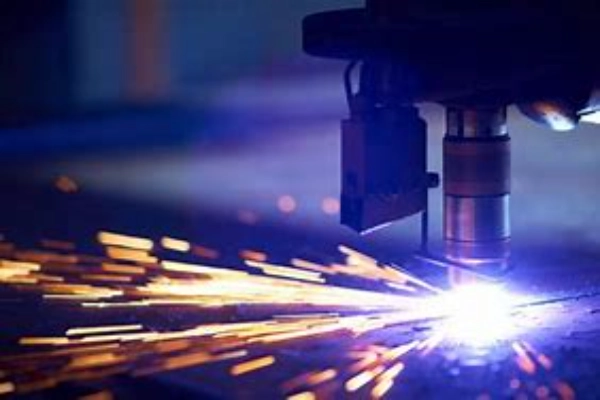
Medical and cosmetic applications: Er:Glass is used in skin treatments, while Nd:YAG is widely applied in laser spot removal and tattoo removal.
Industrial processing: Yb:YAG is commonly used in laser welding and cutting, while neodymium-doped glass is suitable for laser ranging.
Conclusion
Laser glass and laser crystals each have their own advantages and are suited to different applications. Glass, with its low cost, large size, and flexible doping, is ideal for high-energy laser systems, while crystals, with their high thermal conductivity, high gain, and optical stability, are better suited for high-power and precision laser applications. In the future, advancements in materials science, composite laser media, and novel fabrication techniques will further enhance the performance of these materials, opening new possibilities for laser technology.
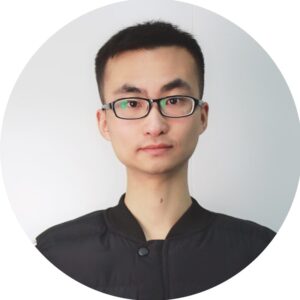
Frank
Frank graduated from the University of Shanghai for Science and Technology, majoring in optics. As a technical engineer at Crylink Company, he deeply understands crystal materials and laser components.
Related Video(s) with this Article
Related Product(s) with this Article
Related Application(s) with this Article