Introduction:
Introduction: Delving Into Optical Films and the Four Cornerstone Technologies. In the vast and evolving realm of modern optics, optical films stand out as unsung heroes. These micro-thin layers, often invisible to the naked eye, serve as the backbone to myriad applications we interact with daily. Imagine staring at a computer screen, watching a laser show, or simply wearing a pair of sunglasses. Behind these seemingly diverse applications lies the silent efficacy of optical films, ensuring that light behaves just as intended, whether that means enhancing clarity, filtering harmful rays, or creating visual spectacles.
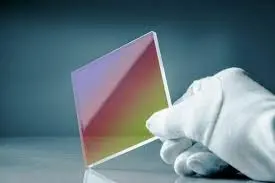
As pivotal as these films are, their performance is not purely a result of their material composition. Instead, it’s the unique coating technologies employed during their fabrication that dictate their final characteristics. Different technologies can lead to variations in film thickness, uniformity, adhesion, and even the way they interact with light. Therefore, understanding these technologies is akin to unlocking the secrets behind the optimal performance of optical films.
This article embarks on a detailed exploration of four major coating technologies that have left indelible marks on the world of optics: thermal evaporation, ion-assisted deposition, ion beam sputtering, and magnetron sputtering. Each method, with its distinctive approach and benefits, contributes to the diverse range of optical films that power our modern world. Join us as we demystify the science and art behind these cornerstone technologies, revealing the precision and innovation that drive the optics industry forward.
Principles of Each Technology
Thermal Evaporation: Traditional yet Trustworthy
A time-tested method, thermal evaporation, is often hailed as the foundation stone of many modern coating technologies. Rooted in the simplicity of physics, this method banks on the principle of transforming solid materials directly into vapor. When materials are subjected to high temperatures within a vacuum chamber, they bypass the liquid state, transitioning straight to vapor.
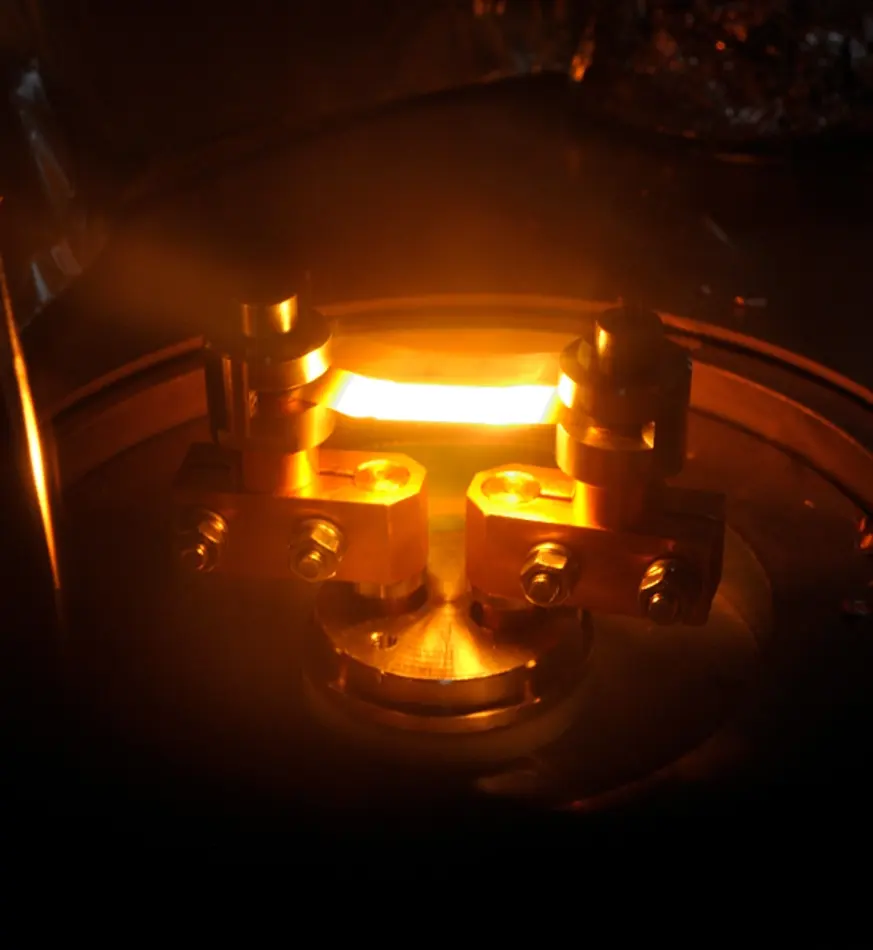
This vapor then travels unimpeded, thanks to the vacuum, and settles onto a cool substrate. As it does so, it forms a coherent and often highly reflective thin film. Historically, thermal evaporation has been pivotal in industries requiring consistent, albeit simpler, coatings such as anti-reflective layers on eyeglasses and certain optical filters.
Ion-Assisted Deposition: The Interplay of Ions and Atoms
Beyond traditional methods, science sought ways to further refine film quality. Enter ion-assisted deposition, a technique that merges the foundational concepts of evaporation with the dynamic influence of ions. As material evaporates in the traditional sense, a concurrent stream of ions bombards it. These ions compact the settling particles, leading to films that are not just denser, but also more resilient to environmental adversities.
Additionally, this method affords the luxury of tailoring refractive indices, enabling specialized applications like beam splitters and specific wavelength filters in high-tech industries.
Ion Beam Sputtering: Precision at its Peak
For applications demanding unparalleled consistency and precision, ion beam sputtering is the go-to choice. At its heart, this method involves an ion source that shoots high-energy ions at a target. On impact, these ions trigger a cascade, dislodging atoms from the target. These displaced atoms then journey onto a substrate, amassing as an ultra-precise film. What sets ion beam sputtering apart is its meticulous control. Every parameter, from ion energy to deposition rate, can be finely tuned, enabling repeatable results that are invaluable for high-end optical components and research applications.
Magnetron Sputtering: The Power of Plasma
Technology Comparison: Navigating the Pros and Cons
Thermal Evaporation
In the annals of coating technology, thermal evaporation emerges as a tried-and-true method, owing to its simplicity and cost-effectiveness. Requiring straightforward equipment, it becomes particularly economical when dealing with smaller-scale production endeavors. With time, this technique has built a reputation for reliability. However, it does come with its set of drawbacks. The method offers a restricted palette of materials, which may, at times, lead to a compromise in the film quality. But for applications that demand single-layer coatings without complex requirements, thermal evaporation proves adequate. Furthermore, when considering the costs, especially for smaller batches, this process stands out for its economic viability.
Ion-Assisted Deposition
Rising to prominence for its ability to offer enhanced film properties, ion-assisted deposition holds several advantages. Its main attraction lies in delivering superior film quality that is further accentuated by adjustable refractive indices. Its versatility extends to accommodate a myriad of materials. However, the method does introduce a level of complexity, primarily because of the diverse process parameters it entails. This technology shines when multi-layer coatings are in question, especially for sophisticated optical instruments. On the financial front, the costs are moderate, influenced by the type of ion source and the intricacies of the deposition process.
Ion Beam Sputtering
For those seeking perfection in film deposition, ion beam sputtering stands unparalleled. The hallmark of this method is its exceptional uniformity and pinpoint precision. Every stage of the process is stable and predictable, ensuring replicable outcomes.
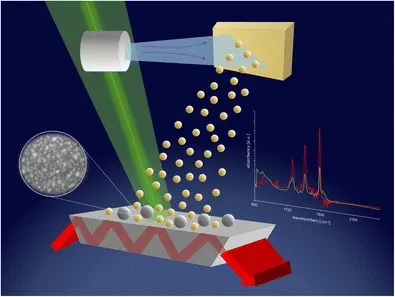
But perfection often comes at a cost—both in terms of time and money. The deposition rates are on the slower side, and the equipment doesn’t come cheap. However, for high-stakes optical applications where accuracy is non-negotiable, the investment in ion beam sputtering is justified. The premium pricing is a reflection of the advanced machinery and stringent process controls.
Magnetron Sputtering
An embodiment of modern coating prowess, magnetron sputtering boasts of high deposition rates. This method not only offers a plethora of material options but also ensures that the films are of uniform thickness. The technique, however, is not without challenges. There’s always a potential for substrate heating, and crafting multi-layer coatings can get intricate. Yet, its applicability spans across various sectors, including electronics, optics, and a range of industrial coatings. When one evaluates the costs, they oscillate between moderate to high, influenced heavily by the design of the system and the magnitude of the operation.
Application Prospects: Envisioning the Future of Coating Technologies
Each technology offers unique potentials:
In today’s rapidly evolving technological landscape, the need for specialized and optimized coatings becomes paramount. Whether it’s for aesthetic purposes, protection, or performance enhancement, coating technologies play a pivotal role in determining the final product’s quality and efficacy.
Thermal Evaporation
At its heart, thermal evaporation is rooted in simplicity, making it a perennial favorite among industries seeking cost-effective solutions. Given its straightforward approach to producing thin films, it naturally finds resonance in applications requiring basic optical enhancements or decorative flair. Manufacturers, especially those constrained by budgetary considerations but unwilling to compromise on quality, gravitate towards this method.
Ion-Assisted Deposition
Entering the scene with a promise of tailoring, ion-assisted deposition offers an unparalleled degree of customization. It empowers industries to craft coatings that cater explicitly to nuanced requirements. Particularly in domains where specific optical characteristics are paramount—like anti-reflective coatings or specialized filters—this method stands as an unrivaled champion. Its adaptability ensures that specialized coatings no longer remain a challenge but rather a standard procedure.
Ion Beam Sputtering
In realms where precision isn’t just desired but essential, ion beam sputtering emerges as the torchbearer. Advanced laser systems, critical research instruments, and other high-end applications demand consistency and precision that’s non-negotiable. Here, ion beam sputtering’s capability to offer repeatability, coupled with its meticulous accuracy, makes it an indispensable asset. Industries aiming to break barriers and redefine limits will find a reliable partner in this method.
Magnetron Sputtering
Riding on the back of the electronics revolution, magnetron sputtering is poised for expansive growth. As devices shrink in size but grow in functionality, the coatings’ role becomes even more vital. Magnetron sputtering, with its promise of uniform and adaptable coatings, is ideally suited to cater to this burgeoning demand.
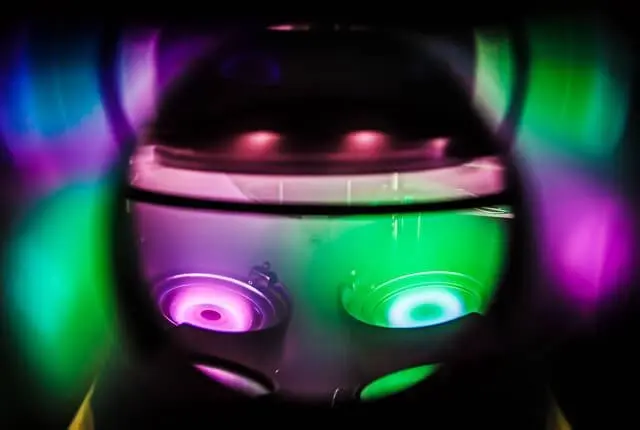
From vibrant displays that dazzle eyes to intricate sensors that capture the minutest of changes, this technology promises to be the backbone of tomorrow’s electronic marvels.
Conclusion: Pioneering the Future of Optical Films
The journey of optical film preparation showcases the ingenuity of engineering and science collaboration. While each technique offers unique merits, the collective evolution promises advancements that cater to an array of applications, ensuring that optical films continue to be integral in shaping technological horizons.
FAQs
- 1.What materials can be used in thermal evaporation?
Predominantly metals, though some organic materials can also be used depending on their evaporation temperatures. - 2.How does ion-assisted deposition improve film adherence?
The concurrent ion bombardment during deposition enhances film-substrate interaction, ensuring better adherence. - 3.Why is ion beam sputtering considered a ‘clean’ process?
The absence of filaments or hot parts reduces contamination, making the films ultra-pure. - 4.Can magnetron sputtering handle complex multi-layer coatings?
Yes, with the right process controls, multi-layer coatings are achievable, albeit with some complexity. - 5.Which technology is best for anti-reflective coatings?
Ion-assisted deposition is often preferred due to its ability to customize refractive indices, crucial for anti-reflective coatings.
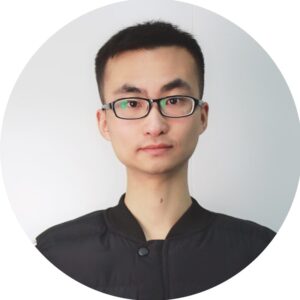
Frank
Frank graduated from the University of Shanghai for Science and Technology, majoring in optics. As a technical engineer at Crylink Company, he deeply understands crystal materials and laser components.
Related Video(s) with this Article
Related Product(s) with this Article
Related Application(s) with this Article